Plastic extrusion for reinforced, durable materials
Plastic extrusion for reinforced, durable materials
Blog Article
Understanding the Fundamentals and Applications of Plastic Extrusion in Modern Manufacturing
In the realm of modern-day production, the technique of plastic extrusion plays an important role - plastic extrusion. This intricate procedure, entailing the melting and shaping of plastic through specialized passes away, is leveraged across different markets for the development of diverse products. From auto parts to durable goods product packaging, the applications are substantial, and the capacity for sustainability is just as excellent. Unwinding the basics of this process reveals real versatility and capacity of plastic extrusion.
The Fundamentals of Plastic Extrusion Refine
While it may appear complicated, the principles of the plastic extrusion process are based on relatively straightforward principles. It is a production process where plastic is thawed and after that formed right into a continual account via a die. The raw plastic product, frequently in the form of pellets, is fed into an extruder. Inside the extruder, the plastic is subjected to heat and pressure, causing it to thaw. The liquified plastic is after that required with a designed opening, called a die, to develop a long, continuous product. The extruded product is cooled and after that reduced to the preferred length. The plastic extrusion process is extensively used in numerous sectors because of its flexibility, cost-effectiveness, and efficiency.
Various Kinds Of Plastic Extrusion Methods
Building upon the fundamental understanding of the plastic extrusion procedure, it is necessary to check out the numerous techniques included in this production approach. The two main techniques are profile extrusion and sheet extrusion. In profile extrusion, plastic is melted and created into a continuous profile, often utilized to develop pipes, poles, rails, and home window structures. On the other hand, sheet extrusion develops huge, level sheets of plastic, which are typically additional refined right into items such as food packaging, shower drapes, and auto components. Each technique calls for specialized equipment and exact control over temperature and stress to make sure the plastic keeps its form throughout cooling. Comprehending these strategies is vital to using plastic extrusion effectively in contemporary manufacturing.

The Role of Plastic Extrusion in the Automotive Industry
A frustrating majority of parts in modern-day lorries are products of the plastic blog extrusion procedure. Plastic extrusion is largely made use of in the production of numerous vehicle components such as bumpers, grills, door panels, and control panel trim. Thus, plastic extrusion plays a crucial duty in automotive manufacturing.

Applications of Plastic Extrusion in Consumer Product Production
Past its substantial effect on the automobile sector, plastic extrusion shows similarly efficient in the world of consumer products making. The flexibility of plastic extrusion enables manufacturers to develop and generate complex shapes and sizes with read the full info here high accuracy and performance. The flexibility, adaptability, and cost-effectiveness of plastic extrusion make it a favored selection for many customer goods producers, adding significantly to the market's development and innovation.
Environmental Effect and Sustainability in Plastic Extrusion
The prevalent use of plastic extrusion in manufacturing welcomes analysis of its environmental ramifications. Effective machinery lowers power usage, while waste management systems recycle scrap plastic, lowering raw material demands. In spite of these improvements, better technology is required to mitigate the ecological impact of plastic extrusion.
Conclusion
In verdict, plastic extrusion plays a crucial duty in contemporary manufacturing, particularly in the automobile and customer items sectors. Understanding the essentials of this procedure is key to enhancing its advantages and applications.
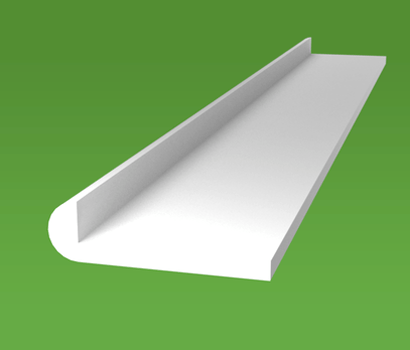
The plastic extrusion process is extensively made use of in numerous sectors due to its effectiveness, cost-effectiveness, and versatility.
Building upon the standard understanding of the plastic extrusion procedure, it is needed to explore the various strategies entailed in this manufacturing method. plastic extrusion. In comparison, sheet extrusion develops big, level sheets of plastic, which are generally more refined right into items such as food packaging, shower drapes, and automobile parts.An overwhelming bulk of components in contemporary automobiles are products of the plastic extrusion click now procedure
Report this page